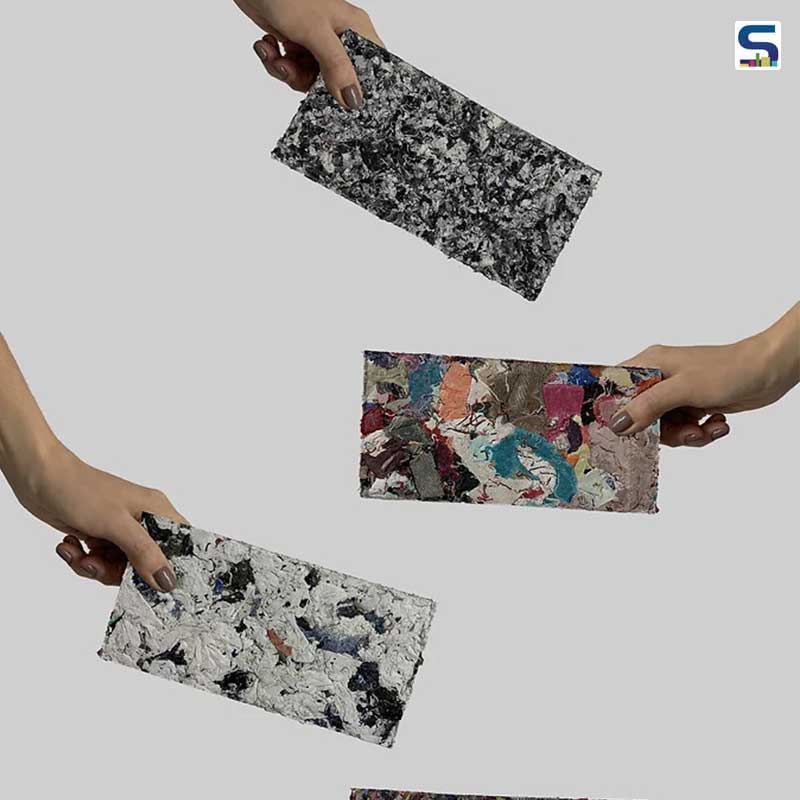
Despite being known for glitz and glamour, the fashion industry is one of the leading polluters. A report from the UN Environment Programme suggests that the fashion industry alone is responsible for an estimated 8 per cent of global carbon emissions, with 92 million ton of solid waste and 20 per cent of global wastewater per year. With this rate, the global annual construction waste, by comparison, is expected to reach 2.2 billion ton by 2025.
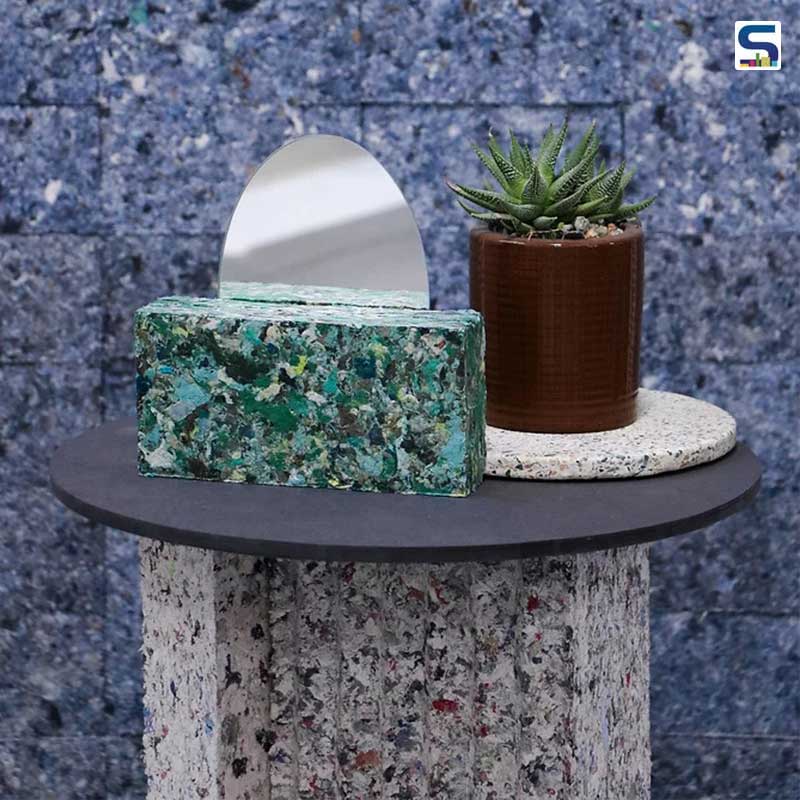
French architect Clarisse Merlet developed an idea for her school project to curb this problem without even releasing its full potential of it. Concerned about the issue of pollution in the construction industry, she started making bricks with waste from plastic bottles, cardboard and eventually textile. This led to the formation of FabBRICK in 2019, where she turned her idea into a proper construction material that offers reliable technical performance and a unique visual appeal. “To achieve this goal, we send companies the textile waste they produce back, after having transformed it into design products or interior fittings so that they can realise how much waste they produce each year,” adds Clarisse Merlet, architect and founder, FabBRICK.
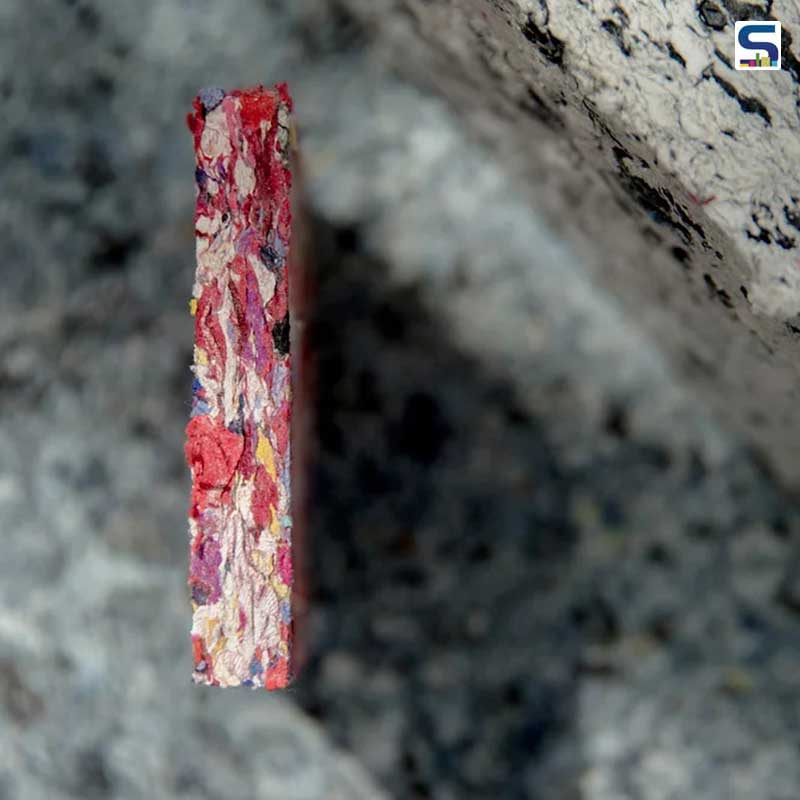
Merlet and the team experimented with different techniques before finding the process that would be used to produce the bricks. They started by compressing the textile into a mould. A crusher is used to transform the textile into fibres and little pieces of fabrics. These fabrics are then mixed with a binding which results in the formation of a clay-like material that can be later shaped in a mould.
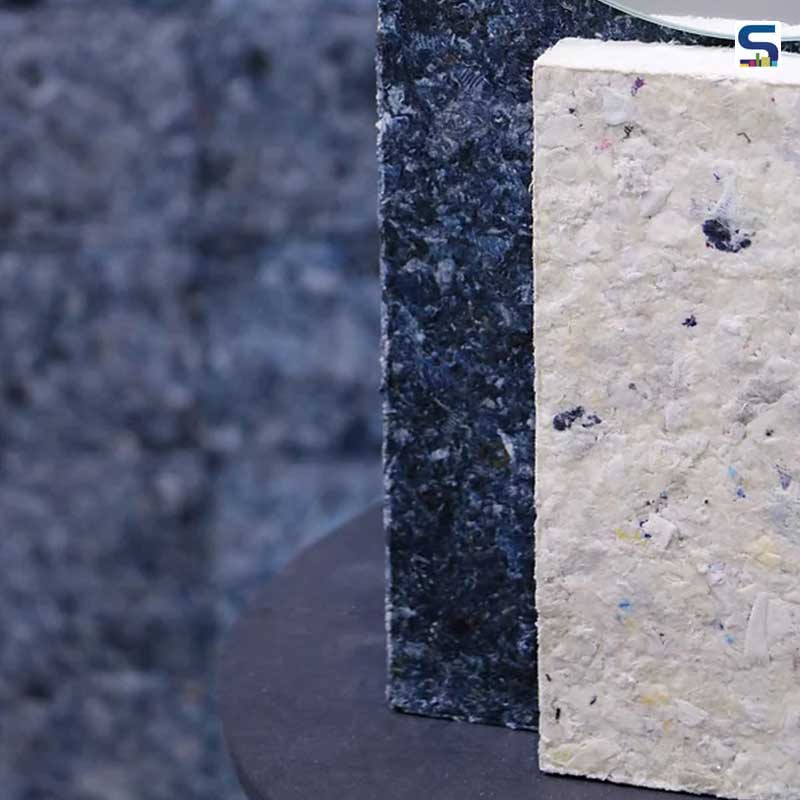
The designing process takes place in steps. The first step begins with accepting discarded clothes at their studio in Paris where the pile of clothes is sorted by colours. Merlet informs that for each project, the customer chooses the format and the colour. FabBRICK has developed around 10 different sizes, and as they do not dye their bricks, the colour is obtained by the textile they use. The textile is then shredded to obtain three shapes of fibre, namely, 7 mm, 20 mm and 40 mm. Depending on the project, the size is picked. Made from 100 per cent ecological ingredients, rot-proof glue is made, which is then mixed in the fibres by hand. The mixture is weighed every time to make sure each brick has the same density. It takes about 30 mins to shape the mixture into a brick once it is set to mould in the machine, which can produce 200 bricks a day. The bricks are dried in ambient air for 10-15 days.
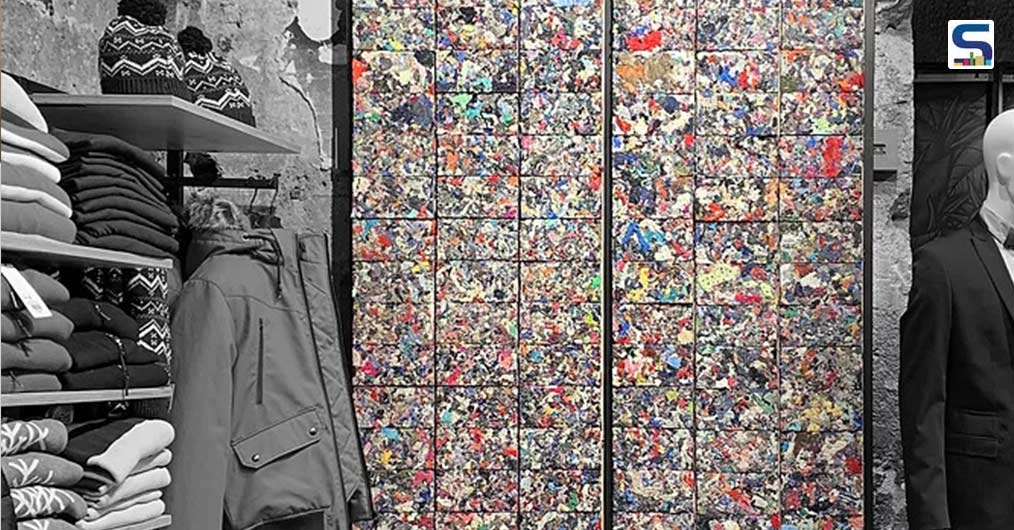
According to Merlet, the brick has a very good mechanical resistance almost like a concrete block. It also has good insulating quality, acoustic and thermal, and is resistant to fire and water. This makes the brick an ideal choice for indoor use including furniture, partition walls and seats.
With a futuristic upgrading, Merlet aims to improve her artisanal manufacturing process to an industrial one. “Today, we can provide all our materials and tools to our clients within a radius of 100 km. Tomorrow we would like to set up a FabBRICK factory in every region and country which produces textile waste,” she informs.
Photographs: Clarisse Merlet; Courtesy: FabBRICK