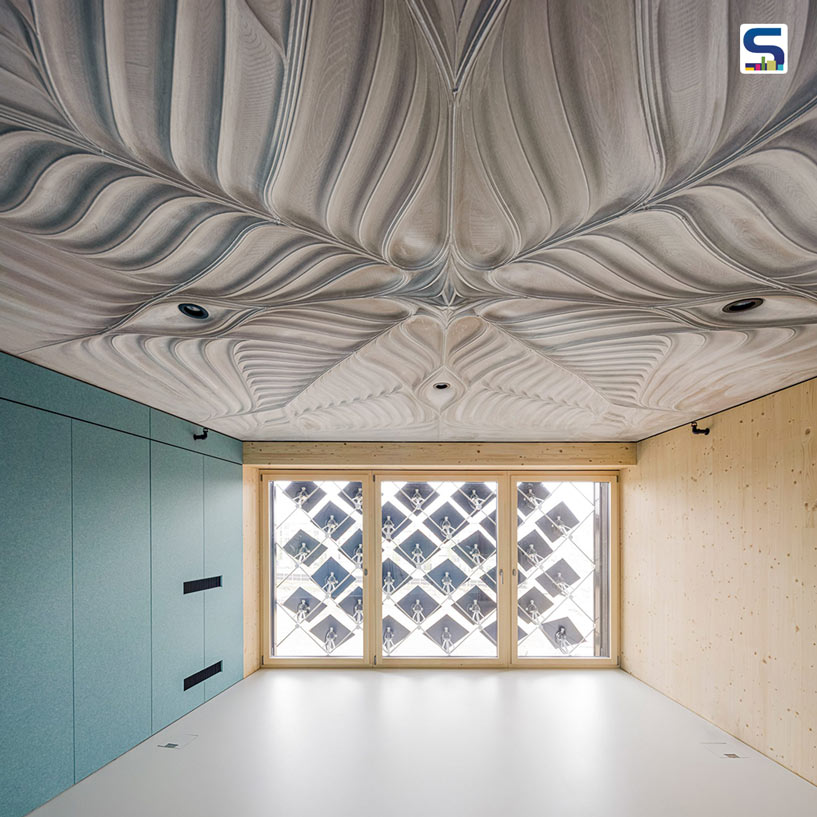
3D Printing technology has allowed designers and architects to think and go beyond the limits of conventional design and building methods. Recently, researchers at technology university ETH Zurich have crafted a deeply ridged ceiling prototype known as HiRes Concrete Slab for its NEST research building-so-called living lab- in the Swiss city of Dübendorf using 3D printing and casting. The team claims that the ceiling saves energy along with being aesthetically pleasing. The striking ceiling has been installed within the two-story ‘HiLo unit,’ an office space used by robotic researchers. Read more about this below at SURFACES REPORTER (SR):
Also Read: ETH Zurich Creates Precast Concrete Slab by 3D Printing Mineral Foam| SR Material Update
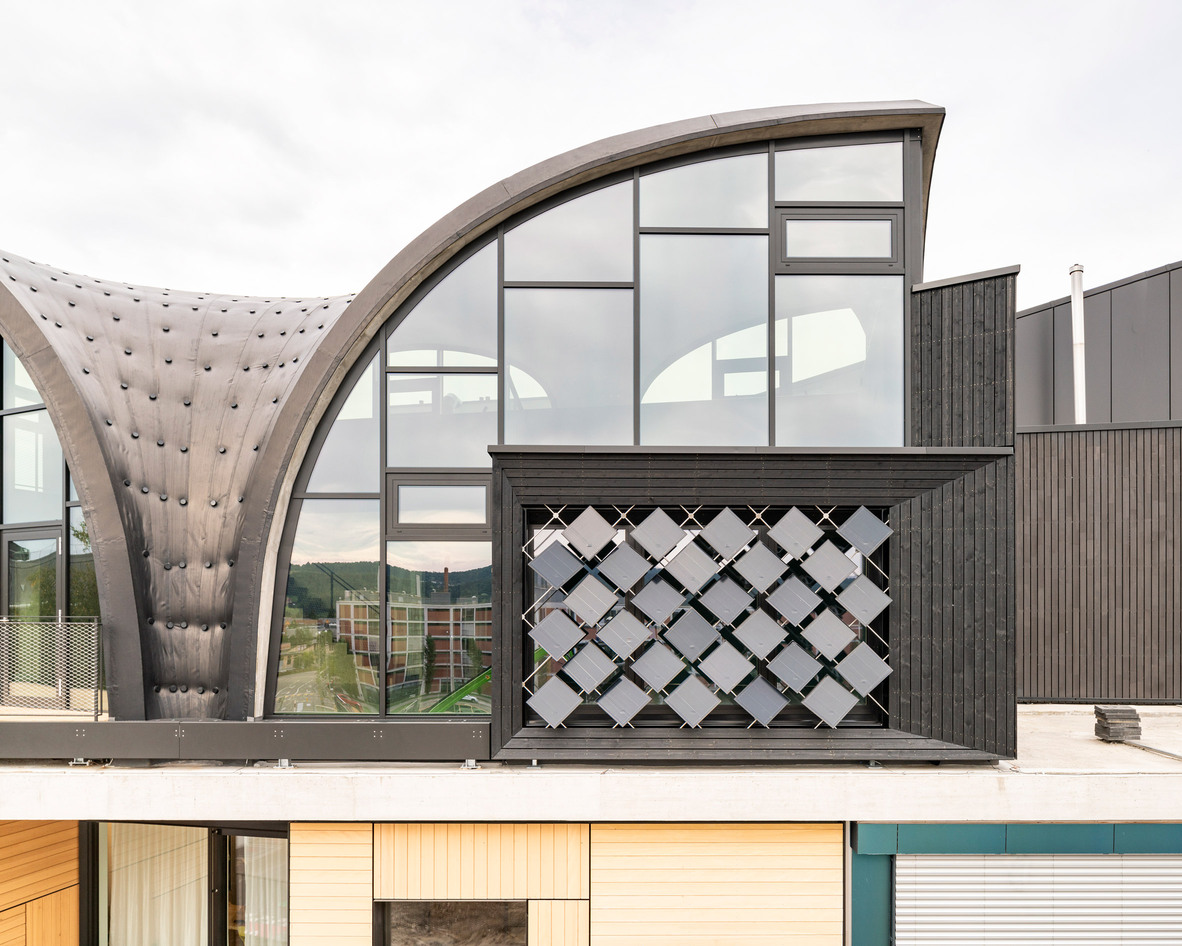
The thin shell concrete slab is fashioned by ETH Zurich's Digital Building Technologies (DBT) in partnership with its Block Research Group (BRG) and Architecture and Buildings Systems (A/S).
3D-Printed Framework
The eye-catching slab was formed by casting concrete in situ in a 3D-printed mould. It was crafted to exhibit the benefits of using 3D-printed formwork, such as integrated building services, material reduction, and the amazing aesthetics of free form.
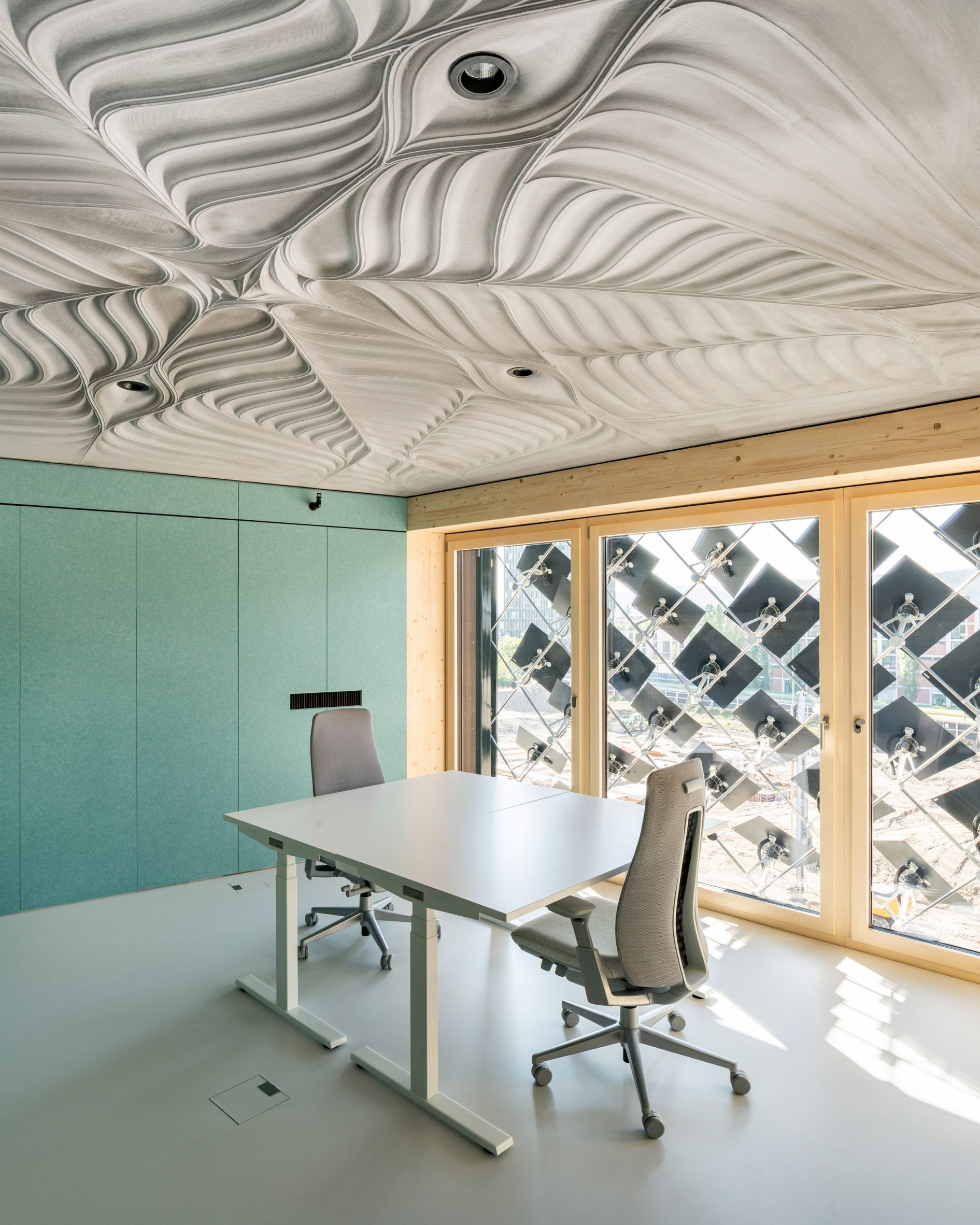
How It Was Created?
The team poured concrete into 43 thin 3D moulds to form the intricate ceiling. The thickest contours on the slab are seams where these moulds meet. A laser-cut wooden waffle supports these moulds.
The creation of concrete slabs requires minimal materials and allows the research team to integrate cooling, heating, ventilation and other building services during the construction process.
The construction method requires a minimal amount of material and enabled the researchers to integrate building services such as heating, cooling and ventilation during the construction process. The team 3D printed four ventilation ducts with polymer and set them into the structure before the concrete was poured.
Energy-Efficient Design
The researchers claimed that the grand design lowers operational energy. The geometry of 3d-printed ventilation ducts integrated into it is designed to use airflow and lower mechanical energy. The aerodynamic geometry of these ducts makes them more energy-efficient than standard systems. Along with that, the contour patterning on the slab is done by heating and cooling loops of hydronic pipes that all are designed by the A/S team. The resulting surface is very luminous and shows better thermal performance than traditional flat slabs. The computational programming helped to create the pattern that met the required criteria and form a balanced composition.
Along with using the contours of thermal performance, the team ensured that the concrete form would fit within the 3D-printing box and that it could be easily removed from the mould. The thickness of the slab is just 50 millimeters, while its thickest contours are 25 mm wide and 300mm deep.
Also Read: ETH Zurich Creates Precast Concrete Slab by 3D Printing Mineral Foam| SR Material Update
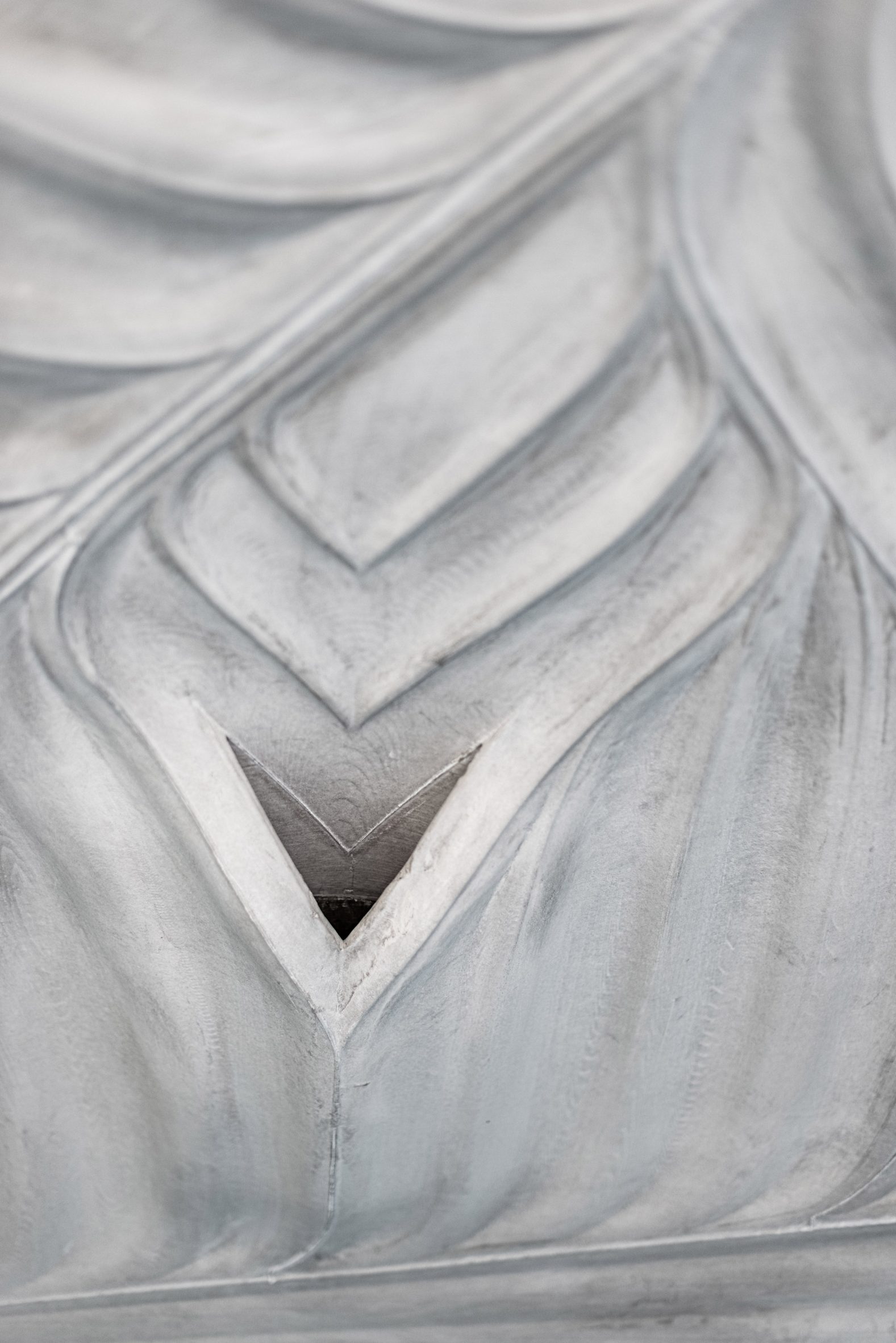
Use of 70 Percent Less Concrete
The concrete slab is a thin, doubly curved funicular shell, which helps to ‘transfer all the loads through pure compression," said the design team. "Designing the vault to only take compression forces plays to the strengths of concrete, which is weaker in tension." Its vaulted shape takes advantage of concrete’s high compressive strength and thus the structure requires less material.
Four tension tied one on each corner of the slab to withstand the horizontal force produced by the arch. Thus, the structure results in a 70 percent reduction of material compared to a traditional reinforced concrete slab.
EMPA Robotics team installed the concrete slab in the office ceiling. The concrete ceiling also contains holes for light fittings.
The entire slab is assembled as a group of parts that easily combine together. The seams between each part are read as the most arresting contours, proposing a continuous, seamless surface.
Project Details
Project Name: HiRes Concrete Slab
Location: NEST Research Building by ETH Zurich, Dübendorf, Switzerland
DBT Team (development, design, and fabrication): Andrei Jipa, Angela Yoo, Georgia Chousou, Prof. Dr. Benjamin Dillenburger
Project Partners: Block Research Group, ETH Zürich: Dr. Matthias Rippman, Francesco Ranaudo, Dr. Tom Van Mele, Prof. Dr. Philippe Block (structural design), Architecture and Buildings Systems, ETH Zürich: Dr. Gearóid Lydon, Prof. Dr. Arno Schlueter (integrated building systems), ROK Architects: Michael Knauss, Silvan Oesterle (unit architecture)
Photo Courtesy: © Andrei Jipa
Keep reading SURFACES REPORTER for more such articles and stories.
Join us in SOCIAL MEDIA to stay updated
SR FACEBOOK | SR LINKEDIN | SR INSTAGRAM | SR YOUTUBE
Further, Subscribe to our magazine | Sign Up for the FREE Surfaces Reporter Magazine Newsletter
Also, check out Surfaces Reporter’s encouraging, exciting and educational WEBINARS here.
You may also like to read about:
3D Printing- The Future Ahead
3D Printing Homes: A blog around 3D printing and building homes
Is 3D Printing the Future of the Manufacturing Ecosystem?
And more…