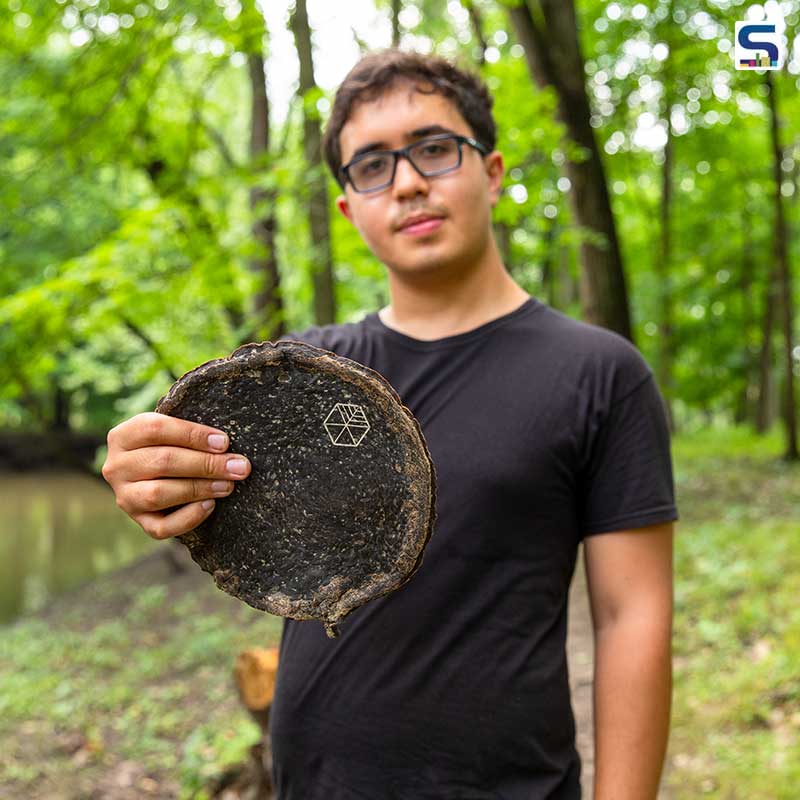
Nature and design can beautifully coexist if embraced properly. And it is our young generation that has taken up the task at hand to balance the elementals of the environment with the rise in climate change. One such green warrior is Gabe Tavas, who recently bagged the American James Dyson Award for ingeniously creating an alternative wood substitute made from kombucha brewing waste called Pyrus. Little did Tavas know, a university submission for the Biodesign Challenge (BDC) – an education programme and competition – would further inspire him to create a substitute for wood. Reminiscing on his experience, he narrates, “I was inspired by a growing field called Biodesign. BDC runs an annual competition in which students from around the world are encouraged to pull insights from nature and use living organisms to create more environmentally conscious products. I helped organise my university’s (University of Illinois) first-ever entry in this competition after I attended the BDC summit in 2019. The projects that I saw during that summit left me in awe and convinced me that much of the future of human innovation lies in the intersection of biology and design.”
Gabe Tavas, founder and project manager, Symmetry Wood, LLC shares his journey of making wood without cutting down trees with Surfaces Reporter (SR).
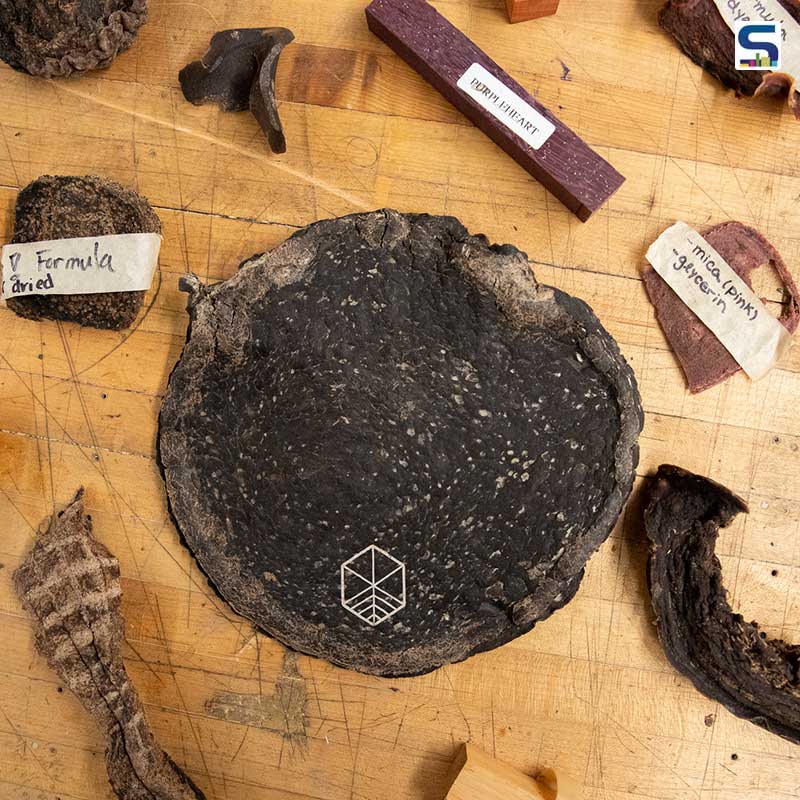
Chemically similar to tree-based wood, Pyrus is a wood-like material made out of bacterial cellulose that is sourced from the kombucha industry.
Pyrus: what it does and how it works
Primarily wood has two essential components, namely cellulose and lignin. While cellulose helps in forming a basic shape and framework, lignin works like glue. Chemically similar to tree-based wood, Pyrus is a wood-like material made out of bacterial cellulose that is sourced from the kombucha industry. A few of these companies use micro-organisms to produce consistent sheets of cellulose on top of the liquid.
Cellulose forms one of the main molecules comprising all forms of wood. The slimy, clear sheets of bacterial cellulose are blended to an even consistency and then embedded in a gel that dries and compresses over several days. During its post-processing, the sheets are placed under a mechanical press to form a flat sheet of wood-like material. Pyrus can be sanded, cut, and coated with resins as needed.
Initially, Tavas stimulated cellulose by feeding cultures of the bacteria with minute quantities of sugar-rich food waste from his university’s dining halls to create real exotic wood. “There was captivation even with the prototype, which could fit in someone’s hand. Although naturally, people wanted to see larger samples before they could imagine constructing finished products with it,” says Tavas, as he recollects the response on creating the prototype.
Furthermore, broadening his horizon, he reached out to initiatives like The Plant and KombuchAid to help improve the process.
Pyrus is hard and brown with a rigid surface that resembles many dense, colourful exotic woods.
Replicating wood without harming the ecosystem
Imitating the physical properties of real wood, Pyrus is hard and brown with a rigid surface that resembles many dense, colourful exotic woods. Saving the need to cut down trees and processing on living trees, Pyrus can be processed on common manufacturing tools like wood saws, laser cutters and CNC machines. However, unaided it is not naturally water-resistant. It can be mixed with additives or coated with standard finishes like shellac to improve its durability. “Also, many exotic kinds of wood are dangerous to cut because they contain extractives that may trigger asthma and skin irritation for the woodworkers who come into contact with their dust. Pyrus, by comparison, does not produce dust that potent, and is therefore safer to work with,” adds Tavas.
For Tavas, the end goal of Pyrus is to replace expensive and fancy wood products which are currently huge drivers of deforestation. Unlike engineered wood which uses compressed sawdust in its production, though relatively waste-free compared to wood, it requires trees to be chopped and processed; Pyrus is made without harming a single tree and is petroleum-free.
Although at present Pyrus is not commercially available in different colours, Tavas and his team have successfully produced coloured samples as part of their research and development.
Pyrus is transformed into small finished products such a functional guitar picks and jewellery which are being sold on Symmetry.
Future of Pyrus
With a little beyond the experimental stage, Pyrus is transformed into small finished products such a functional guitar picks and jewellery which are being sold on Symmetry – another one of Tavas’ creations to fund operations and research. Sharing his excitement over Symmetry, an elated Tavas says, “I had always imagined forming a company from these experiments with bacterial cellulose, so I utilised the resources and entrepreneurial ecosystem of my university to do so beginning in the fall of 2018. Symmetry’s website will cater to woodworkers and designers who are interested in building their well-performing products with a lower environmental impact.”
Now that Symmetry is a legally registered company, the young entrepreneur’s priority is to finish organising its operational structure and settle on a management team alongside leveraging 3D printing to scale up production. “We are recruiting new teammates, seeking new advisors and looking for larger facilities to work out of. Our research is also exploring ways to combine Pyrus with 3D printing to improve manufacturing efficiency and capabilities and reduce the amount of sawdust that woodworkers are exposed to,” he informs.
About the firm
Symmetry aims to create harmony between humanity and nature by creating a sustainable material that can stand in as an alternative to wood. The Symmetry team is comprised of passionate and talented college students with skill sets ranging from material science to sustainable design.
Image courtesy (all images): James Dyson Foundation